- Transport>
Grâce à son nouveau supercargo, Airbus fera voyager les pièces de ses long-courriers par les airs pour augmenter ses cadences de production. Un avion hors-norme, fabriqué sur mesure, avec un soin maniaque, dans l’usine de Toulouse.
Dans un atelier du gigantesque complexe industriel d’Airbus, en périphérie de Toulouse, l’exemplaire no 2 est presque terminé mais n’a reçu que sa sous-couche de peinture, et ressemble à une baleine verte. Le no 3, moins avancé, évoque une coque de navire sur laquelle les « compagnons » – le nom donné ici aux ouvriers ultraqualifiés – fixent patiemment les membrures qui soutiendront plus tard l’énorme « bulle » de tôle.
Quant au no 1, il a déjà pris le large, ou plutôt le ciel. Le BelugaXL, le nouvel avion-cargo d’Airbus, a effectué avec succès son premier vol d’essai, le 19 juillet 2018. Depuis, le cétacé blanc et bleu au sourire espiègle – un décor plébiscité par les salariés de l’avionneur après un sondage mené en interne – survole régulièrement les cieux de la Ville rose avant d’aller faire des virages au-dessus de la Méditerranée.
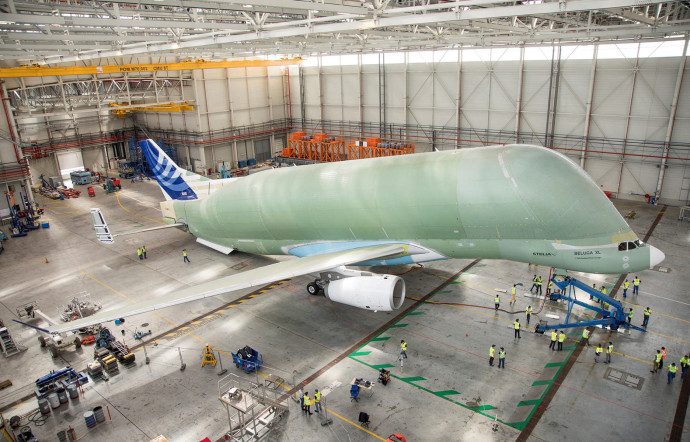
Un vrai puzzle européen
« Nous sommes en pleine campagne de tests, souligne Christophe Cail, chef des pilotes d’essai. Il s’agit de vérifier que l’avion en vol répond aux normes exigées pour sa certification par les autorités européennes, mais aussi de tester le ressenti aux commandes, en nous mettant dans la peau d’un pilote régulier qui devra le manoeuvrer de manière routinière. » L’expérience passager ne sera, en revanche, pas testée. Et pour cause : le BelugaXL est exclusivement destiné à transporter des ailes et des tronçons de fuselages d’avion. Pour comprendre sa raison d’être, il faut se replonger dans l’histoire d’Airbus et de son organisation industrielle.
Avant les années 70, les grands pays européens possédaient chacun leur propre industrie aéronautique. Airbus les a fédérés, mais chacun a gardé certaines prérogatives : la voilure pour le Royaume-Uni, l’empennage pour l’Espagne, le fuselage et l’assemblage pour la France et l’Allemagne…
Dès lors, comment transporter les pièces du puzzle d’un site à l’autre ? La mer, puis la route sont des évidences. Mais ces solutions se révèlent lentes et peu souples. La voie des airs ? Pour cela, il faut un avion à la soute suffisamment vaste. N’en possédant pas, Airbus va se fournir… chez celui qui deviendra son principal concurrent : Boeing.
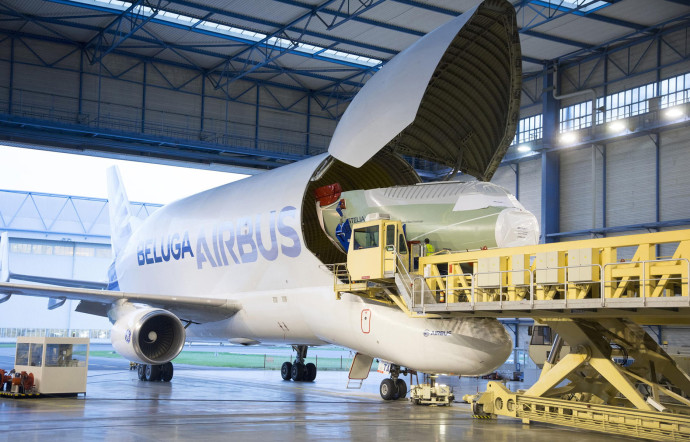
La firme européenne achète le Super-Guppy, un ventripotent quadrimoteur à hélices dérivé du Boeing 377 Stratocruiser, conçu par la compagnie Aerospacelines, et mis en service en 1965 pour transporter les tronçons de la gigantesque fusée Saturn 5 qui devait propulser les astronautes américains vers la Lune. « Airbus produisait à l’époque une vingtaine d’avions par an, puis nous sommes montés en puissance. Quand, dans les années 90, nous avons dépassé les 100 avions, le Guppy était obsolète. Il a fallu lui trouver un remplaçant », explique Bertrand George, directeur du programme BelugaXL.
L’ingénieur en chef est… une femme !
« Je suis un pur produit Airbus ! » Véronique Roca, 51 ans, a réalisé toute sa carrière chez l’avionneur. Diplôme d’ingénieur en poche, elle y entre pour étudier la physique du vol – tous les efforts que supporte un appareil dans le ciel –, ce qui lui offre « la chance d’avoir une vue globale d’un avion ». Après un passage dans le programme A380, elle devient ingénieur en chef sur l’A330 et, finalement, sur le BelugaXL, à la tête d’une équipe qui a atteint 220 personnes. Le 12 juillet 2018, elle signe un document, lourd de conséquences, qui dit en substance : « bon pour le vol ». « Le sommet de ma carrière, même si j’endosse évidemment la responsabilité d’un travail collectif », explique‑t‑elle en appuyant son propos de son regard bleu et déterminé, se félicitant au passage que « la proportion de femmes dans les bureaux d’études augmente, mais c’est un phénomène relativement récent ». Chez Airbus, sur 22 ingénieurs en chef, un quart sont des femmes.
Le camion des airs
Airbus opte alors pour la conception maison de son premier camion des airs, le Beluga ST, sur la base d’un A300. Depuis, cinq exemplaires effectuent trois vols quotidiens entre les différents sites : par exemple entre Toulouse – où sont fabriquées les parties inférieures et supérieures des ailes –, Broughton, en Angleterre – où elles sont assemblées –, Brême, en Allemagne – où elles reçoivent leurs dérives –, et retour à Toulouse pour l’assemblage au fuselage…
Mais l’avion se révèle à son tour sous-dimensionné au début des années 2010. Car il y a un nouveau venu dans le catalogue d’Airbus : l’A350, un long-courrier ultramoderne avec des ailes longues de 28 mètres chacune et mesurant près de 6 mètres dans leur plus grande largeur, fabriquées non plus en métal mais en matériaux composites.
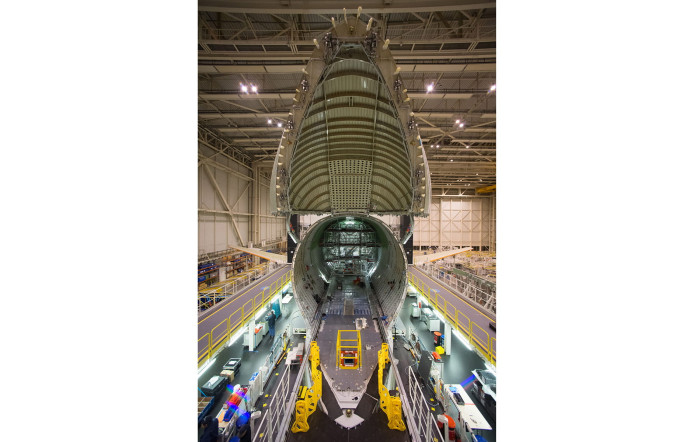
Le défi concerne ici davantage le volume que la masse. Or, dans le Beluga ST, on ne peut loger qu’une aile d’A350 à la fois, placée à 45 degrés. Résultat : des durées de transport multipliées par deux, et l’obligation de remettre sur la route des pièces d’autres Airbus pour faire place à l’A350. Un nouvel avion, plus large et plus haut, était nécessaire pour engranger deux ailes d’A350 à la fois, ainsi que davantage d’éléments des autres modèles. L’objectif : 30 % de capacité de transport supplémentaire. Seul l’énorme A380 affiche des dimensions telles que ses pièces continueront à être acheminées par la mer et par la route.
Le BelugaXL en chiffres
• 63,1 m de long.
• 60,3 m d’envergure.
• 18,9 m de haut.
• 8,8 m de diamètre.
• 53 tonnes de capacité.
• 4 000 km d’autonomie.
Astuce, réactivité, interactivité
« Nous avons opté pour un Beluga augmenté, que nous avons nommé BelugaXL, dérivé de l’Airbus A330 et fabriqué au coût le plus serré possible en réutilisant au maximum des éléments que nous possédons et maîtrisons déjà, déclare Bertrand George. Le challenge, c’est une fabrication sur mesure beaucoup plus “artisanale” que notre production classique. »
Le programme est lancé en novembre 2014, porté par une équipe de concepteurs, puis de techniciens, entièrement dédiée. « On reçoit un fuselage d’A330 sans aucun équipement. On en découpe la partie supérieure à la scie circulaire, avec une précision d’un millimètre sur soixante mètres de long ! Ensuite, on installe tous les renforts », explique Frédéric Vaissière, responsable industriel du programme BelugaXL. Les pièces rajoutées ont été fabriquées à façon par de petites entreprises ou des filiales d’Airbus.
La partie la plus critique, la pointe avant, a été construite par la firme Stelia Aerospace et consiste en une gigantesque porte étanche maintenue par 24 crochets actionnés par un système hydraulique. Tout doit être assemblé avec une précision extrême. « Il y a beaucoup d’ajustage sur la chaîne du Beluga, contrairement aux autres modèles dont la production est plus standardisée », souligne Frédéric Vaissière.
Le positionnement de tous les éléments est contrôlé par laser. Après dix mois de labeur et 250 000 rivets pour fixer les tôles, l’avion passe au poste 2, où il est soumis à de nombreux essais pendant plus de deux mois. Le luxe d’une petite série : seulement cinq appareils seront fabriqués, un par an, jusqu’en 2022. Comment un tel défi a-t-il été relevé ? « Astuce, réactivité, interactivité », résume Véronique Roca, ingénieur en chef du programme.
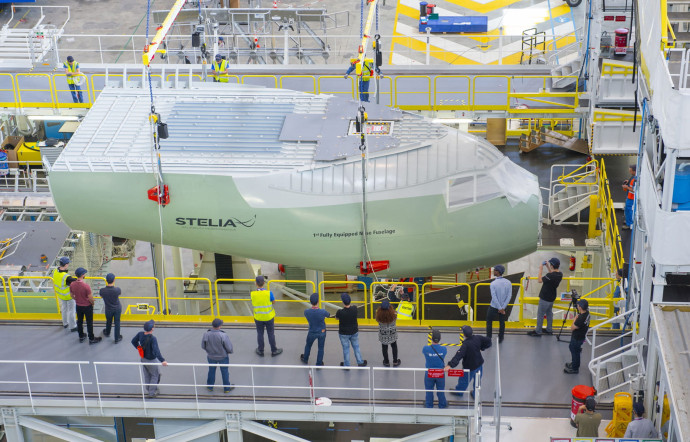
Astuce, lorsqu’il s’agit de trouver les solutions les moins coûteuses et les plus efficaces : surélever la dérive arrière de 2 mètres, puis ajouter des dérives auxiliaires et ventrales pour tenir compte de l’écoulement de l’air généré par l’inhabituel fuselage ; fixer la bulle en concevant chacun des supports sur mesure pour assurer une parfaite distribution des charges ; fabriquer des enceintes spéciales pour certains équipements qui pourraient mal supporter une soute qui n’est pas pressurisée, au contraire de celle de l’A330, ce qui a évité de concevoir de nouveaux équipements avec les coûts qui en résultent.
Réactivité, de la part de l’équipe de production, qui a assemblé l’avion prototype dans des délais record. Enfin, l’interaction entre les équipes : « comprendre l’interface entre chaque métier est primordial pour la réussite du projet. Les ingénieurs sont tous les jours au pied de l’avion aux côtés de ceux qui le fabriquent », précise Véronique Roca. La certification européenne du BelugaXL est prévue pour cet été, et la mise en service, avant la fin 2019.
Les trois premiers exemplaires voleront en tandem avec les Beluga ST, avant que ces derniers ne soient retirés du service chez Airbus et revendus. Le coût du projet ? No comment… « C’est un gros investissement, justifié par la souplesse que nous devons avoir dans les transports entre nos différents sites. Le BelugaXL est conçu pour trente ans et répondra aux éventuelles évolutions de la production aéronautique, souligne toutefois Bertrand George. C’est aussi une aventure humaine et industrielle unique, vitale pour Airbus. »