- The Good Business>
Le site de Crewe, à une trentaine de kilomètres au sud de Manchester, abrite l’ensemble de la production des luxueuses Bentley, de la conception au développement, et à la fabrication. Ici, tout respire l’excellence dans une atmosphère so… British. The Good Life a fait le tour de ce lieu exceptionnel.
Plus de 1 800 demandes d’emploi s’empilent chaque année sur les bureaux des ressources humaines du site de Crewe (dans le nord-est de l’Angleterre), alors qu’il n’accueille « que » 4 000 personnes. C’est dire tout l’intérêt encore porté à la marque Bentley, à son savoir-faire et à sa notoriété. Ici, à quelques miles de Manchester, les places sont chères, d’autant que le turn-over se veut quasi inexistant. En février dernier, Bentley Motors a été reconnu, par le Top Employers Institute, comme l’un des meilleurs employeurs pour la sixième année consécutive. Une mention qui reflète l’attention que l’entreprise porte au développement personnel et aux conditions de travail de ses salariés.
L’usine abrite même plusieurs générations de familles alentour : parfois Crewe voit passer dans ses ateliers du grand-père au petit-fils, ou petite-fille. Une sorte d’institution. Et pour cause, la maison Bentley représente l’un des summums de la qualité et du raffinement anglais. La simple visite de ce site de fabrication – difficile de parler d’usine tellement tout respire le luxe et l’artisanat – apporte une sensation de jubilation, et de respect aussi. Car, depuis le musée jusqu’aux bureaux de la R&D, chaque secteur ou atelier dévoile son lot d’étonnement, de surprise et d’admiration. Ici, la rapidité n’est pas de rigueur. Les hommes s’attachent avant tout à un travail empreint de perfection. Pour preuve, s’il faut 10 heures pour construire une Clio, une Bentayga, le SUV de Bentley, en requiert une centaine. Certes, le gabarit des véhicules n’est pas comparable, mais, surtout, le soin apporté à la fabrication de l’ensemble des pièces et à l’assemblage des modèles se veut totalement différent.
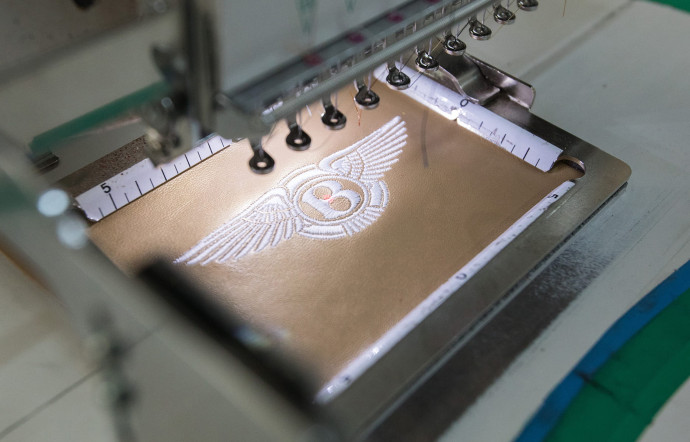
Un travail d’orfèvre
Rien que pour la marqueterie, les professionnels embauchés sur cet atelier effectuent trois jours d’entraînement avant d’accéder à un poste sur la ligne de production. Car le bois, avec le cuir, est l’un des matériaux maîtres de la beauté de l’intérieur d’une Bentley. Pour une qualité optimale des dix finitions proposées, rien n’est laissé au hasard. La quête débute par le choix des sites abritant les arbres exotiques, qui poussent jusqu’à 200 ans avant d’être récoltés et replantés. De ces arbres est extraite la loupe servant à confectionner les faisceaux de placage. Les experts Bentley vérifient chaque fragment de ces placages de 0,6 mm d’épaisseur, une opération qui peut représenter deux journées pleines, avant de valider leur envoi à l’usine. A Crewe, ils sont recueillis dans une cave spéciale dont la température de 17 °C et l’humidité de 56 % restent soigneusement stabilisées et contrôlées en permanence.
Au moment de la confection d’une pièce d’habillage de la voiture, seules les zones de placage les plus homogènes et représentant une esthétique particulière sont retenues. Les opérations d’assemblage et de finition se révèlent minutieuses : application sur le substrat (fondation de noyer, de cerisier ou de chêne), ponçage, laquage, durcissement pendant 72 heures, puis de nouveau ponçage et polissage avant le montage sur le véhicule. L’atelier accorde un mois à la confection de l’ensemble des habillages bois d’une seule voiture ! Digne des meilleurs spécialistes de marqueterie ou d’ameublement.
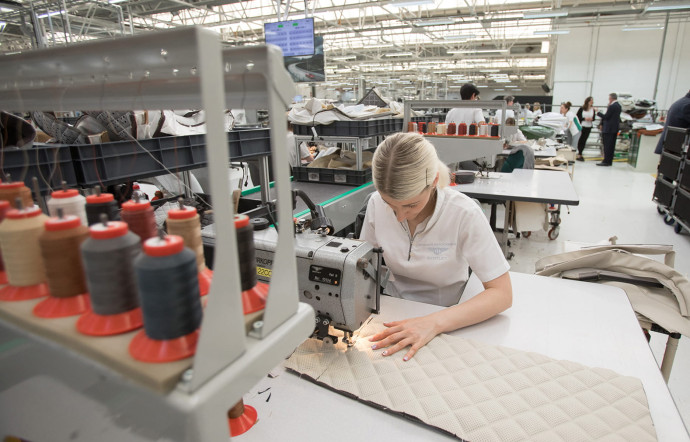
Autre département spécifique à Crewe : celui de la préparation du cuir. Forcément, le soin dédié à la sélection des peaux équivaut à celui consacré à la marqueterie. Un point tout aussi important pour l’habillage de l’intérieur des véhicules, et pour les sensations liées au bien-être et au toucher des matériaux. Ici, 3 000 peaux de taureaux passent dans les mains des 90 couturiers et préparateurs, chaque semaine. Elles proviennent de bêtes du nord de l’Europe, où le climat tempéré et l’absence de clôtures barbelées permettent des cuirs exempts d’imperfections causées par les rayures ou les insectes. Et même si la première sélection se veut déjà très fine, à l’atelier, chaque pièce est de nouveau vérifiée à l’œil et les plus belles parties sont sélectionnées avant la découpe de précision.
Chaque élément est ensuite clouté, façonné et fini à la main. Un façonnage qui requiert du savoir-faire et du temps : six minutes sont nécessaires pour broder une pièce en cuir (4 760 points de couture), alors qu’un siège demande, lui, 20 heures de travail. Chaque jour, l’atelier produit la sellerie pour les sièges, les portes et d’autres accessoires pour quatre Mulsanne, le vaisseau amiral de Bentley. Sur les 400 heures nécessaires pour construire ce fleuron de la marque, environ 150 sont consacrées à la réalisation de l’intérieur en cuir.
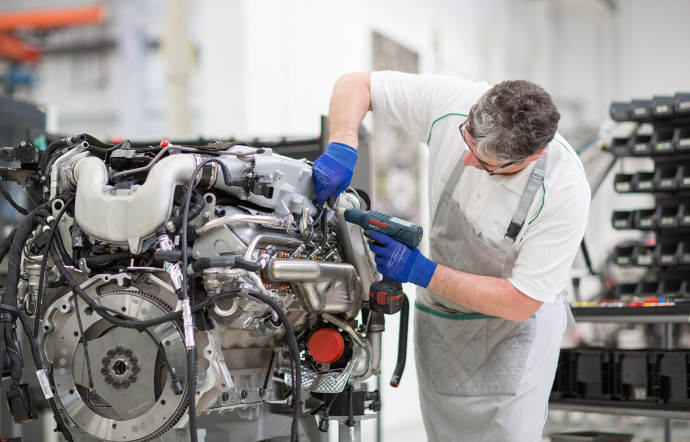
Bentley : puissance et équilibre
Et l’un des fondamentaux d’une voiture dans tout ça, à savoir son moteur ? Crewe abrite, au sein de Pyms Lane, la production des moteurs W12 de 6 litres et V8 à double turbocompresseur de 6 litres. Chaque cœur de Bentley est fabriqué à la main par une petite équipe de techniciens spécialisés. Et les composants, à l’image de tous ceux d’une Bentley, sont finement sélectionnés et analysés, afin de concevoir un ensemble équilibré dans un souci de fonctionnement parfait et durable. Sept mille moteurs W12 sortent de cette ligne pour tout le groupe Volkswagen, qui en a fait son centre d’excellence pour l’intégralité de la production de ce moteur depuis 2014. Ces blocs sont ensuite acheminés vers l’atelier principal d’assemblage. Cette immense partie de l’usine regroupe 700 employés sur deux lignes de fabrication : une dédiée au SUV Bentayga, et la seconde, à la berline Flying Spur et au coupé Continental. Leur rôle consiste à réunir tous les éléments : fixation du moteur sur le châssis à l’aide de 29 boulons, câblage électrique, tableaux de bord, habillages intérieurs, assemblage de la grille emblématique sur ailes avant, installation des roues, du pare-brise, des sièges…
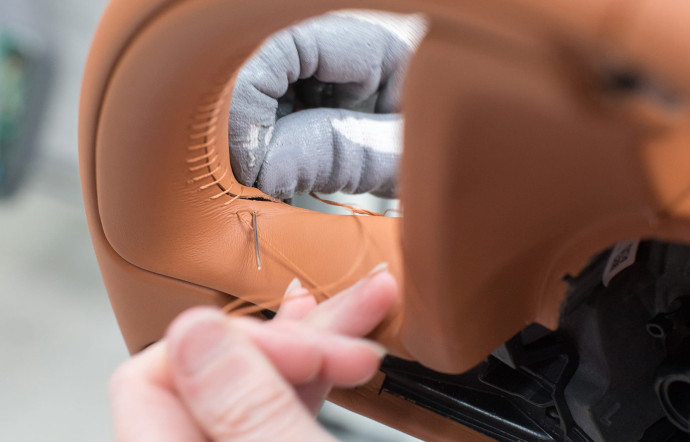
A toute épreuve…
La berline Mulsanne bénéficie, elle, d’une zone de montage séparée. Fabriquée à la main, elle réclame 400 heures de travail aux 83 employés de l’atelier Body in White [« corps en blanc », à cause des combinaisons blanches portées par les ouvriers, NDLR]. Bentley y a investi pas moins de 30 millions d’euros. Cette voiture ultraluxueuse utilise 570 kg d’acier et d’aluminium, et 5 800 points de soudure. Ses monteurs sont chargés d’un assemblage très soigné, notamment en ce qui concerne l’insertion du joint de la partie arrière dans la carrosserie, afin que celui-ci soit totalement invisible.
De même, une grande importance est accordée au coloris d’une Bentley. Et si, dans les 120 proposés par la marque, aucun ne reflète la personnalité du client, Bentley en produira un spécifique. Une fois la carrosserie protégée contre la corrosion, la peinture est pulvérisée à la main en multiples couches. Elle est ensuite recouverte d’une laque, puis poncée et polie à la laine d’agneau pendant 12 heures afin d’obtenir la fameuse finition Bentley Mirror.
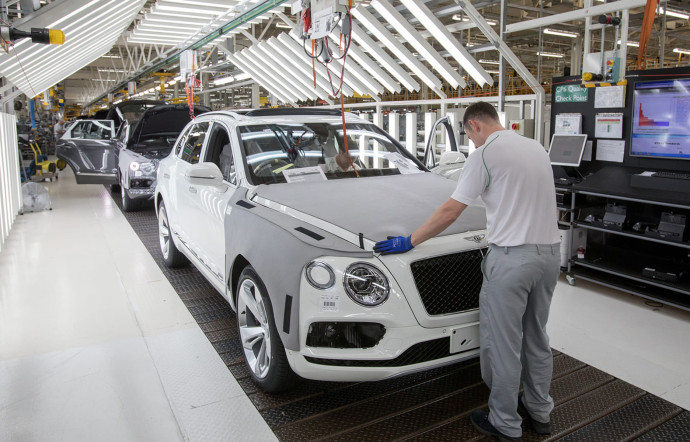
Et pour être sûr d’une excellence optimale pour chaque véhicule, Bentley a mis en place entre 500 et 600 points de contrôle qualité de haut niveau. Et en fin de ligne, toutes les Bentley sont vérifiées minutieusement à l’œil. Hors de question de laisser la voiture à l’arrêt : l’ensemble de cet examen s’effectue lors d’une séance de roulage de plus de 6 kilomètres sur une piste d’essai, puis de plus de 20 sur les routes alentour. Les essayeurs s’assurent que chaque pièce remplit bien son rôle, mais aussi que chaque son et chaque vibration correspondent en tout point à la qualité requise par la marque.
Pour éprouver son étanchéité, chaque voiture passe le test de « mousson » : une pulvérisation de 1 820 litres d’eau teintée d’un colorant UV, suivie d’une vérification sous une lumière UV. Ultimes points de contrôle, un test d’étanchéité, puis le tunnel léger dans lequel la voiture est inspectée une dernière fois, avant d’être déclarée opérationnelle. De quoi partir en toute sécurité, à son volant !