- Horlogerie>
L’institut de recherche TAG Heuer frappe fort : il y a quelques semaines, elle présentait son nouveau modèle Carrera Calibre Heuer 02T Tourbillon Nanograph, équipé d’un spiral en carbone. Une première mondiale ! The Good Life est allé à la rencontre de Guy Sémon, directeur général de ce laboratoire hors norme.
The Good Life : Cela fait quinze ans que vous êtes dans l’horlogerie. Quinze années durant lesquelles vous n’avez pas arrêté de donner des coups de pied dans la fourmilière. Que cherchez-vous à apporter à cette industrie ?
Guy Sémon : Je n’ai pas la prétention d’avoir apporté quoi que ce soit à l’horlogerie. C’est elle qui m’a beaucoup apporté. Je me considère comme un pirate : je passe ma vie dans les laboratoires, je lis des bouquins… Cela me permet de regarder les choses sous un angle différent, de faire des liens, de remettre en cause certains principes.
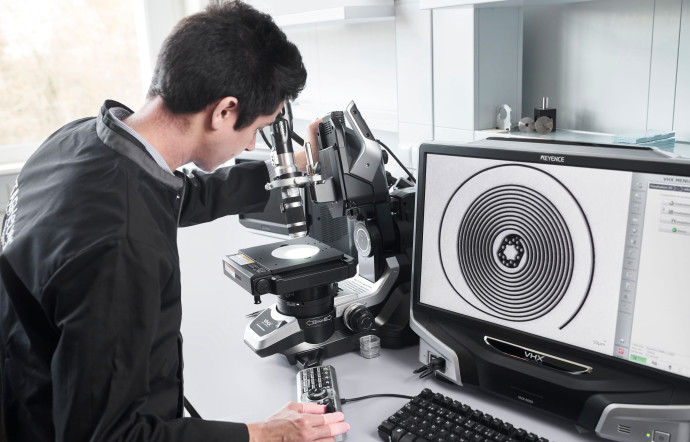
TGL : Un pirate à la recherche du mouvement perpétuel ?
G. S. : Il n’existe pas ! Ce qui m’intéresse, c’est la partie « régulation » de la montre, sa précision, que je souhaite rendre indépendante de la réserve d’énergie disponible. C’est un problème de physique, pas d’horlogerie. Les horlogers ne savent pas qu’ils sont en fait des physiciens ! C’est très complexe et nous n’en sommes qu’au début de l’histoire : il y en a encore pour des décennies d’améliorations possibles !
TGL : Lorsque vous êtes entré chez TAG Heuer en 2004, c’était déjà en qualité de responsable de la recherche et du développement. Etes-vous revenu au même poste ?
G. S. : Non. Je suis aujourd’hui directeur d’un institut de recherche de niveau universitaire. A la différence qu’ici nous avons 25 scientifiques de 12 nationalités, dont les compétences se partagent entre physique et mathématiques. Plusieurs millions sont actuellement investis pour installer, dans les murs de TAG Heuer, à La Chaux-de-Fonds, un laboratoire de pointe. Nous avons commencé l’an dernier et n’avons pas encore tout à fait terminé. A terme, 30 personnes travailleront ici.
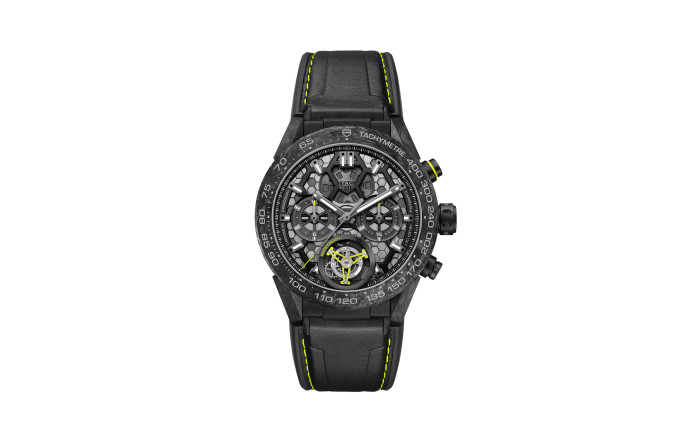
De nouvelles techniques de fabrication des composants
TGL : A sa naissance, en janvier 2018, ce laboratoire était destiné au groupe LVMH. Va-t-il désormais uniquement travailler pour la marque TAG Heuer ?
G. S. : Notre mission est d’apporter notre aide à TAG Heuer, bien sûr, mais également aux autres marques du groupe LVMH. Le sujet d’étude est évidemment la montre, mais le potentiel d’inventions dépasse largement le domaine de l’horlogerie !
https://youtu.be/xCCgR3Qn6_Y
TGL : Qu’y a-t-il dans cet institut ?
G. S. : Des équipements lourds. Nous avons, par exemple, fait l’acquisition d’un microscope atomique à sonde ionique, d’un microscope électronique à transmission ou encore d’un rayon X spectrométrique. Ce matériel va servir à nos trois départements. Le premier s’intéresse à la physique des solides : nous développons des alliages et des polymères qui doivent nous permettre d’inventer de nouvelles techniques de fabrication des composants. Le deuxième traite de mécanique avancée : nous tentons de repenser des systèmes mécaniques avec des approches novatrices, notamment celle des mécanismes flexibles, basée sur l’élasticité de la matière. Ici, nous utilisons beaucoup la modélisation et la simulation. Enfin, nous avons également un laboratoire de physique des nanoparticules : c’est de ce département que sort le spiral en carbone présenté en début d’année dans la Nanograph.
Un processus de fabrication très complexe
TGL : Pourquoi vous être attaqué au spiral ?
G. S. : Chez TAG Heuer, nous sommes très fiers d’être une manufacture. Mais il nous manquait la maîtrise de cet élément clé. Avec ce projet, nous entrons dans le club très fermé des fabricants de régulateurs.
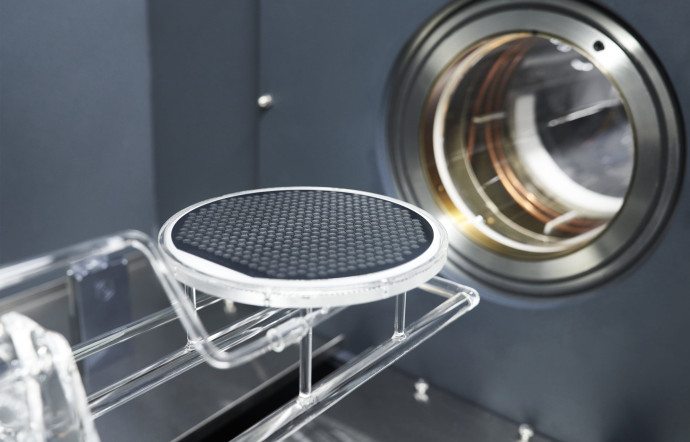
Un parcours hors des sentiers battus
Guy Sémon a pour le moins un parcours atypique pour un horloger – qu’il n’est pas, d’ailleurs. Ingénieur de formation, il teste, entre 1983 et 1988, tout ce que l’armée de l’air française met au point d’objets volants. Revenu à la vie civile, ce natif de Montbéliard est professeur de mathématiques et de physique à l’université de Besançon, spécialisé dans la mécanique des fluides et la modélisation des turbulences.
Il se met ensuite à son compte, proposant son expertise dans la simulation de vol pour hélicoptères, avions de combat et missiles. Ses clients sont notamment EADS et Lockheed Martin. C’est au hasard d’une rencontre dans un avion qu’il doit son entrée chez TAG Heuer, d’abord comme consultant, puis chargé de mettre en place une cellule R&D entièrement dédiée à la Monaco V4. Cette pièce remplaçait pour la première fois une partie des rouages par une courroie. Puis ce sera le Mikrographe, en 2010 (un chronographe au 1/100 de seconde), le Mikrotimer Flying 1000, en 2011 (1/1 000), le Mikrogirder, en 2012 (5/10 000), ou encore le Pendulum, en 2013 (équipé d’un échappement magnétique). Son credo : la montre n’est qu’un système physique, composé d’une réserve d’énergie, d’une transmission et d’une boîte à vitesse.
Une conception de l’horlogerie avec laquelle il n’aura de cesse de bousculer les lignes établies. Nommé directeur général de TAG Heuer en 2014, il finit par revenir sur le terrain – ou plutôt dans le labo –, avec sa nomination à la tête de l’Institut de recherche TAG Heuer en janvier 2018. « Il y en a encore pour des décennies d’innovations horlogères. »
TGL : Mais vous auriez pu vous équiper pour la fabrication de spiraux traditionnels…
G. S. : Les spiraux en alliage métallique ont deux inconvénients : ils sont très efficaces en ce qui concerne la compensation thermique, mais ils sont très sensibles aux champs magnétiques. Ceux-ci modifient leur géométrie et compromettent leur précision. De plus, le processus de fabrication est très complexe, donc cher. La matière doit être transformée, puis façonnée. A la suite de quoi les composants doivent être assemblés et réglés à la main.
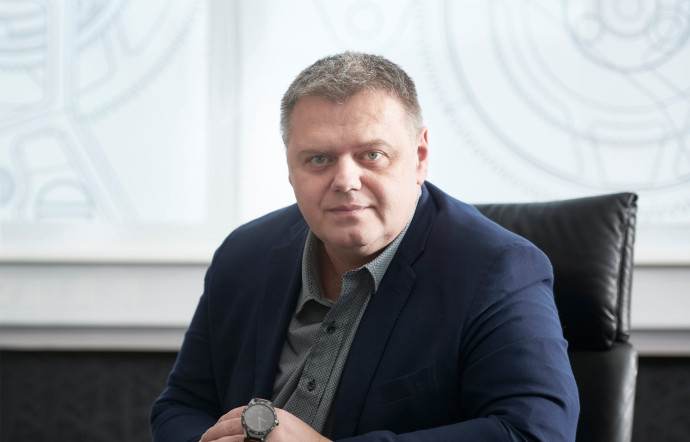
De nombreux brevets
TGL : … ou en silicium ?
G. S. : Cette solution ne nécessite en effet pas d’assemblage, la production est efficiente et le spiral est amagnétique. Mais le silicium reste très fragile. Il casse comme du verre lorsque la montre tombe au sol. Une telle chute équivaut à 2 000 G. Or, nos montres doivent résister à des chocs de 5 000 G. Enfin, la technologie autour de ces développements est protégée par de nombreux brevets.
TGL : Comment en êtes-vous, dès lors, arrivé au carbone ?
G. S. : L’histoire débute en 2013. Je travaillais sur un autre projet, pour lequel j’avais besoin d’un matériau particulier : il devait se comporter comme un polymère insensible au magnétisme, tout en ayant une structure atomique semblable aux métaux. Or, il n’existait pas ! En visitant un laboratoire aux Etats-Unis, je suis tombé sur une expérience avec des nanotubes de carbone. Cette matière n’est pas récente, elle date des années 80. Mais elle est extrêmement intéressante : des feuilles de graphène formant un réseau hexagonal sont enroulées sur elles-mêmes. Les cristaux cylindriques ainsi obtenus ont une rigidité très élevée et une large déformabilité. Cela ne m’avançait pas pour mon projet, mais j’ai tout de suite vu des possibilités dans le domaine des spiraux.
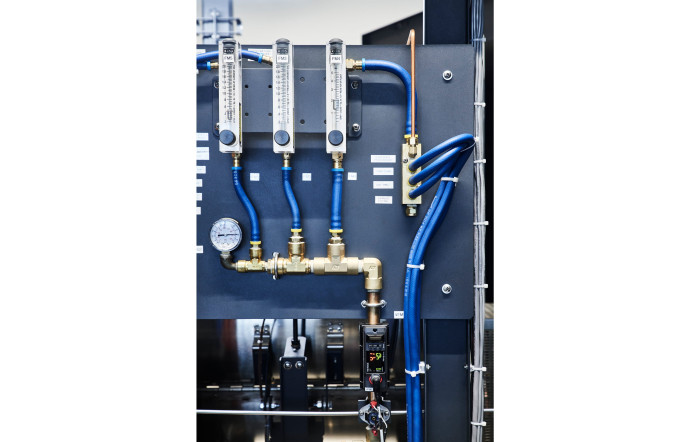
TGL : De quelle manière fabrique-t-on un spiral en carbone ?
G. S. : A l’intérieur d’un réacteur chimique, que nous avons dû développer spécialement. Il n’en existe pas d’autres dans le monde !
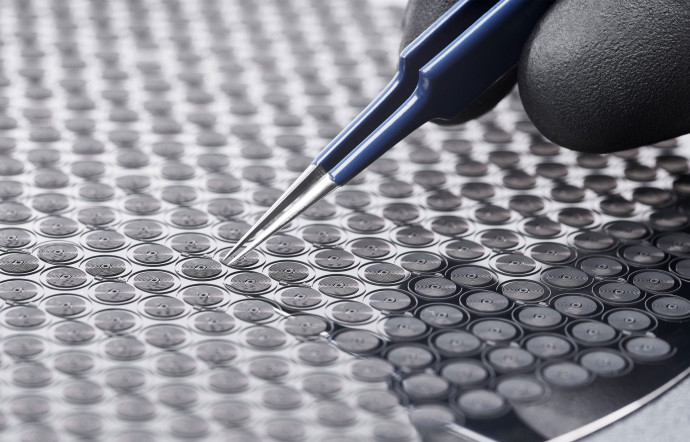
150 000 pièces par année
TGL : Comment cela fonctionne-t-il ?
G. S. : Nous utilisons une plaque de silicium, non pas pour le matériau en lui-même, mais parce qu’il est extrêmement plan et propre. Cette plaque est placée à l’intérieur du réacteur sous vide, dans lequel on fait circuler de l’éthylène, un gaz chargé en carbone et utilisé pour la fabrication des nanotubes. Grâce à la méthode du « dépôt chimique en phase vapeur », les spiraux – jusqu’à 300 par plaque – vont alors croître, atome par atome, durant quatre heures. Mais les nanotubes sont constitués à 96 % de vide. Dernière étape : il faut encore remplir ce vide en y injectant d’autres atomes de carbone. Au final, on obtient un matériau composite, dans lequel sont associés des nanotubes de carbone et du carbone.
TGL : Ces spiraux sont-ils déjà en production ?
G. S. : Oui, nous avons commencé la production en série pour la Nanograph. Avec deux réacteurs, nous avons une capacité de 150 000 pièces par année.

Lire aussi
Horlogers belges, leur tactique du tic-tac
Bell & Ross + Renault, dans les starting‑blocks
Swatch : un hommage au Louvre en quatre montres personnalisables !