- Inspirations>
Equipementier et logisticien dans le secteur aéronautique, Daher est devenu par « alliance » le plus ancien avionneur du monde encore en activité. Visite de l’une de ses usines, celle de Tarbes, où sont fabriqués ses fameux TBM.
Au loin, les Pyrénées, enneigées en cette saison, dessinent la ligne d’horizon. On aperçoit l’usine avant même d’atterrir. Ses nombreux bâtiments jouxtent littéralement les pistes de l’aéroport. Rien d’étonnant à cette proximité, le site Daher de Tarbes fabrique des équipements et des systèmes pour les plus grands programmes aéronautiques mondiaux, d’Airbus à Gulfstream en passant par Dassault Aviation ou Embraer.
Il est entré dans le giron de Daher en 2009, lorsque le groupe familial a racheté la Société pour la construction d’avions de tourisme et d’affaires (Socata), auparavant Morane-Saulnier – du nom de pionniers de l’aviation –, créée en 1911. Cette acquisition vaut aujourd’hui à Daher le titre d’avionneur le plus ancien du monde encore en activité. Daher, pour sa part, a vu le jour en 1863 dans le transport maritime et le négoce de produits de fonderie, avant de se diversifier progressivement dans les services pour le nucléaire, puis la logistique et l’équipement aéronautique.
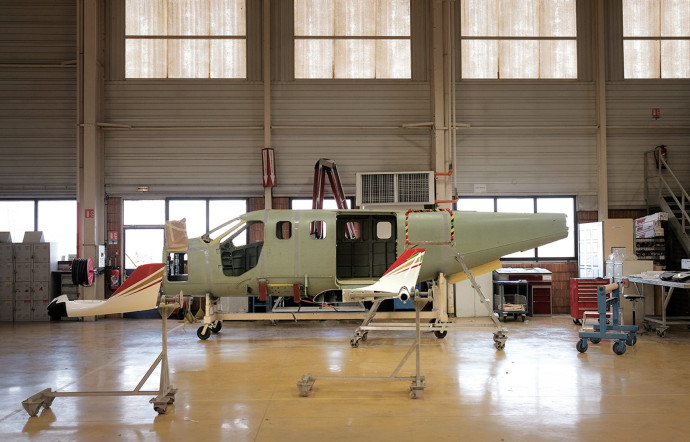
L’usine de Tarbes construit en moyenne 55 avions chaque année. Elle produit actuellement les TBM, dont il existe aujourd’hui deux versions, le TBM 930 et le TBM 910, lancés respectivement en 2016 et en 2017. C’est un monoturbopropulseur pressurisé qui transporte cinq passagers en plus du pilote. Il se situe entre les avions monomoteurs de type Cessna ou Piper, qui ne sont pas pressurisés, et les jets de type Honda ou Falcon. Contrairement à ces avions à réaction, généralement pilotés par un professionnel, le TBM est très prisé de ceux qui veulent être aux commandes. « C’est comme pour une Porsche ou une Harley-Davidson, quand il possède un TBM, le propriétaire, qui est très souvent pilote, n’a pas envie de s’asseoir à l’arrière », remarque Philippe de Segovia, directeur marketing produit de la division avions de Daher.
Les compagnons à chaque étape
Un appareil n’entre en fabrication que s’il a été commandé. Le client peut personnaliser son TBM à la commande via une application ou dans le showroom de l’usine. Il choisit le motif et les couleurs extérieures de son avion ainsi que le coloris du cuir des sièges, du tapis et des tablettes. Du début de la construction à la livraison au client, il faut compter de sept à huit mois. La fabrication démarre par l’assemblage des 21 cadres qui composent le fuselage. Tout est en aluminium sauf la cloison en titane qui isole le moteur. Le squelette est monté cadre par cadre, puis le revêtement est « épinglé » sur cette structure pour être mis en tension et prendre sa place avant d’être encollé, épinglé à nouveau, puis riveté.
Le site de Tarbes en chiffres
• Métiers : construction des avions TBM 930 et TMB 910, et fabrication d’équipements et de systèmes pour l’aéronautique.
• Effectif : 1 500 personnes.
• Site : 53 ha dont 10 couverts, site contigu à l’aéroport Tarbes-Lourdes-Pyrénées, 12 lignes de production.
• Production : pour les programmes Airbus, ATR, Boeing, Bombardier, Dassault Aviation, Embraer, Gulfstream.
• Construction : en moyenne, 55 avions TBM par an, soit près de 19 % du marché mondial de l’aviation générale (non commerciale), estimé à 300 appareils par an.
• Délai : de sept à huit mois sont nécessaires entre la commande d’un TBM et sa livraison au client.
• Un avion TBM contient 50 000 rivets, 22 000 références de pièces, 80 km de câblage et pas moins de 40 kg de peinture.
• Prix d’un TBM : de 3,9 à 4,2 M €.
A chaque étape, les compagnons (comme on nomme les ouvriers dans le monde aéronautique) intègrent les câbles, l’hydraulique, les hublots, etc. Les deux parties de l’appareil, l’avant et l’arrière, sont ainsi construites en parallèle puis jointes pour former le fuselage. « Nous avons conçu des bâtis verticaux. Cela permet aux compagnons de toujours travailler à hauteur d’homme, à l’intérieur ou à l’extérieur de la structure », explique Philippe Joseph- Edmond, chef de ligne fuselage et premier compagnon à avoir travaillé sur le projet TBM.
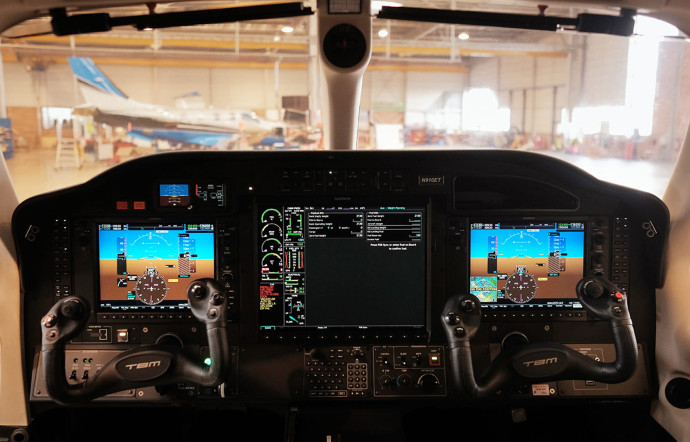
Après huit semaines, le fuselage est devenu une structure, prête à passer à l’atelier de peinture, tout comme la voilure. La structure et les ailes sont poncées puis peintes, d’abord en blanc mat et ensuite selon les choix du client. Il faut compter environ soixante-douze heures pour chaque couche – jusqu’à huit couches peuvent être nécessaires. Au final, l’avion s’est « alourdi » de 40 kilos de peinture. Vient alors la FAL, la final assembly line, sur laquelle il reçoit ses équipements électriques, planche de bord, climatisation, volants et logiciels. Les ailes, l’empennage, le moteur et l’hélice sont à leur tour fixés à la structure. Après l’habillage intérieur, il est prêt pour les vols d’essai et la vérification de ses performances.
« Le client vient en prendre livraison après un vol d’acceptation réalisé avec notre chef pilote. Environ 80 % des TBM sont destinés à des clients aux Etats-Unis, où nous leur convoyons l’avion en deux jours », précise Pascal Bellocq, responsable de la peinture et de la FAL.
Faire face à une demande croissante
Comme tous les avionneurs, Daher sous-traite certaines pièces nécessaires pour ses avions, mais il en fabrique lui-même une bonne part. D’autres bâtiments du site de Tarbes abritent différentes lignes de production d’équipements, notamment une usine composites qui confectionne, entre autres, les trappes de train d’atterrissage des Airbus A350. La part des matériaux composites dans l’aéronautique ne cesse d’augmenter.
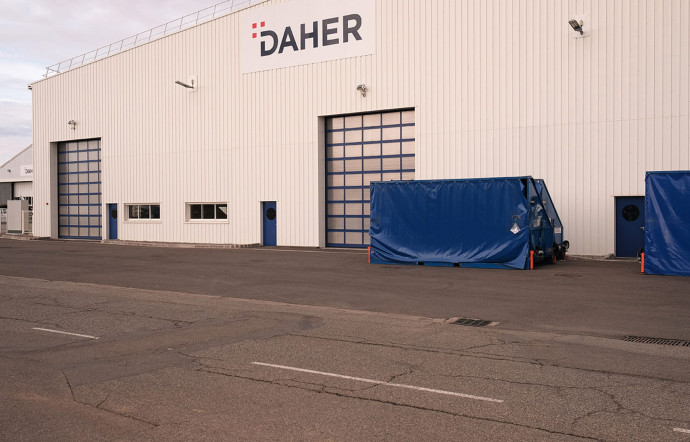
Pour faire face à une demande croissante, Daher s’est équipé de machines performantes pour la découpe, le drapage, le moulage et la cuisson des pièces. Pour les trappes de l’A350, l’usine de Tarbes utilise le système robotisé de la PME bretonne Coriolis Composites pour le placement du matériau sur de grandes surfaces complexes. « Pour la polymérisation, nous disposons d’auto claves de 4 mètres de diamètre et 12 mètres de long, capables de traiter les pièces les plus imposantes, comme des ailes ou des trappes de train d’atterrissage », explique Thomas Mensac, responsable de la fabrication des composites.
Les trappes sont assemblées sur la ligne de montage, où elles passent de poste en poste jusqu’à la finalisation. Pour cette ligne, un bâtiment de 5 000 m2 a été construit. Les pièces composites droite et gauche des trappes sont traitées en parallèle. Elles sont équipées des ferrures et des différentes parties nécessaires à leur montage final sur l’avion. Grâce au système robotisé et à la ligne de montage, Daher a réduit la durée du cycle complet des trappes de quarante à vingt-cinq jours. L’usine peut ainsi suivre l’augmentation de la cadence de production, qui passera de 8 à 13 trappes par mois pour répondre aux besoins d’Airbus.
Daher en chiffres
• Date de création : 1863.
• Métiers : constructeur d’avions, équipementier aéronautique et prestataire de services industriels et logistiques.
• Effectif : près de 10 000 personnes en 2018, dont 1 200 personnes proviennent du logisticien Kuehne+Nagel dans le cadre du contrat pour les flux logistiques d’Airbus.
• Président du conseil d’administration : Patrick Daher.
• Directeur général : Didier Kayat.
• Siège social : Marseille, et siège opérationnel à Orlytech.
• Chiffre d’affaires : 1,080 Md € (estimation 2017), auxquels s’ajouteront, en 2018, de 80 à 100 M € du contrat logistique Airbus.
• R&D : 9 bureaux d’études et centres de recherche et développement dans le monde mènent des travaux sur les processus et les matériaux. Le Daher Lab, en France et dans la Silicon Valley depuis 2017, teste les innovations technologiques et leur adaptabilité aux métiers et aux produits Daher.
• Capital : 87,5 % Sogemarco-Daher (famille Daher) et 12,5 % Bpifrance.
Daher est à la fois avionneur, équipementier et de plus en plus logisticien
« Nous occupons une place unique dans le paysage de l’industrie aéronautique. Nos TBM ne concurrencent vraiment ni les avions légers ni les jets d’affaires, ce qui nous permet d’atteindre une part de 19 % du marché de l’aviation générale non commerciale. De plus, nous travaillons pour la plupart des avionneurs, à qui nous fournissons des équipements, mais à qui nous apportons également de plus en plus de services à valeur ajoutée », remarque Tony Thoma, vice-président marketing et communications de Daher.

Exemple de ces services : un avion A350 sur deux est entièrement assemblé par du personnel de Daher sur les lignes d’Airbus. Autre exemple : la société a gagné un contrat important pour gérer l’ensemble des flux logistiques du groupe Airbus en France, depuis janvier 2018, contrat qui s’élève à environ 100 millions d’euros par an. Elle participe à de nombreux projets en partenariat RSP (risk sharing partnership). Par exemple, les trappes de train d’atterrissage de l’A350 ont été dessinées et mises en fabrication par les bureaux d’études de Daher sur un cahier des charges et un coût par pièce fournis par Airbus.
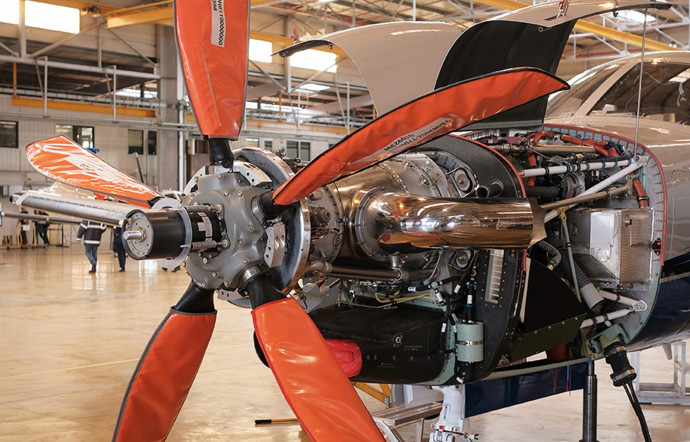
Avec cette montée en puissance de l’ingénierie, Daher envisage l’avenir avec sérénité, même si les nouveaux programmes d’avions seront moins nombreux dans les années qui viennent. « Il y a tout de même 12 000 appareils en commande qu’il faudra fabriquer dans les sept ou huit prochaines années. L’aviation commerciale reste porteuse », affirme Tony Thoma. Dans ce contexte, Daher s’est fixé de nouveaux objectifs dans son plan quinquennal (2018-2022) : devenir franco-américain, ce qui passera probablement par des acquisitions ; et devenir référent dans le numérique en développant des offres pour l’avion connecté, la logistique et la chaîne d’approvisionnement.
Lire aussi
Tanger impose son beat à nouveau et rêve plus grand
Jaeger LeCoultre, la haute horlogerie aux frontières de l’art